What do YOU ask before you begin your Jig or Weld Fixture Design? Here are some questions to start the discussion.
When you are presented with some product parts and asked to design a fixture or jig so they can be welded together, what questions do you need answered before you begin? It is important to get as much information on the project as possible before you even do a rough sketch.
For example:
1) How many parts will be welded together in this one fixture?
The production planning team will need to figure this out. The more parts they can fit on one fixture, the less fixtures and operators they will need. However they need to take into account that if one station in the factory takes longer than the rest of the stations they will be creating a bottle neck that will slow the whole production line. That could be fixed by having two of the same fixture, or by reducing the number of parts welded together in one fixture.
2) Is there another product line with very similar but different parts that could be welded together in the same fixture with a quick change over?
Sometimes a fixture can be used for several products. Just replacing one or two sub assemblies can quickly create a fixture that can run two or more products. In a future blog we will delve into the different gizmos and tools you can use to make the change over fast and easy.
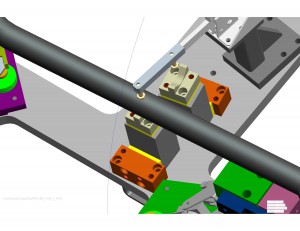
- V-Blocks for two product lines

Designing for two product lines sometimes is easy.
3) Will the fixture be automated or manual?
Will you be using pneumatic clamps or manual? What about sensors that will sense if the part is in place before clamping or before beginning the welding procedure? Will there be forward and back checks?
At Rentapen, our 3D models will show the placement and mounting of the sensors and clamps. The design must allow for room for the hoses and wires. At Rentapen we leave the design of the controls and electrical to the experts. We focus strictly on the mechanical aspect of the fixture. It is important to you and the team that there is a clear understanding of where your responsibility lies. Tasks for who is responsible for what parts of the fixture (jig) or robot cell should be clearly laid out before you begin the design.
4) Will the fixture be trunion or table mounted?
Will it be robotically or manually welded? If it is robotically welded, what are the dimensions within which the fixture must fit?
5) When is the project due?
When should the preliminary design be ready for review? When should the checked drawings be completed? Is there a set schedule?
6) Where are the welds?
The answers to these question should be on the weld drawings for the product. Usually, in a well planned out line, there is a product drawing of the sub assembly produced in the fixture that you are going to be designing. Study the drawing for the location of the welds. If there is no such drawing, ask!
7) What are the critical dimensions?
Study the drawing and identify those dimensions that are held to a tighter tolerance. If there are no tight tolerances between welded parts, then the fixture may not require shimming. It doesn’t hurt to ask to make sure. Asking before you begin is much more efficient.
8) Are there parts that could be put on the fixture wrong?
Study the product assembly and see if you may need to error proof the fixture so that the parts can only go into the fixture in the way they are supposed to. We don’t want them welding something on backwards.
9) Do you have a list of preferred vendors? Some manufacturers prefer Destaco or Parker for their clamps. The larger companies always have a list of the vendors they use and the products they like. For example, Genesis Systems requires all their vendors to use Rentapen’s RAPid Tooling Components (TM) wherever possible to reduce the costs of their weld fixtures.
As a design service company, Rentapen has even more questions to ask.
10) What are your design and detail standards?
We want to match the customer’s standards as best as possible. We put the drawings on the customers format, and follow their standards. We ask for samples of good drawings so that we can see how holes are called off and slots and chamfers are dimensioned.
11) Do you put more than one detail on a drawing?
Some of our customers put everything on the same size format and put as many part details as will fit on D size sheet. Other customers limit it to four details on a D size sheet. And some customers like to have each part detailed on its own sheet. A B C D or E.
12) How often do you want status updates?
For smaller fixtures, you will design it up and only have them look at it once before you start detailing it. But for larger projects, usually the customer will want to see your progress once a week, or as you complete the design for each section of the fixture. I use the term customer to mean who you report to, who you are serving, be it your production planning team or your manager … whoever your customer is. As a fixture designer the best way to reduce costs for your time is to get feedback on your designs before you go too deep.
What questions have I left out? What else do you ask?
Please add to the conversation and let me know what you think!